Attached are slides for Part two of two outlining the advanced topics of printer mechatronics.
Tag Archives: technology
Inkjet Printer Mechatronics Part one of two
Attached are slides for Part one of two outlining the basic printer mechatronics.
Inkjet Printing Mechatronics
Piezo Inkjet Printing Performance
After our previous post on Piezo and thermal print head technology we have had several of our customers stop in and ask about the working principles of the Piezo inkjet print head. In fact one of our largest customers, a siding contractor, places posters printed with this technology for window advertisements because they are durable and resistant to the elements.
Diving into the working principles of how these work can be summarized at a very high level of a deformation mode of either: squeeze, bend, shear, or push.
The squeeze type of piezo print head works by heating a metal plate which transfers heat to the nozzles on two sides to create pressure gradient which forces the droplets out of the print head.
The bend and push methods are similar and work by heating a plate which transfers heat to a reservoir of ink. This increase in pressure again will force the ink out of the print nozzle. The main difference is that bend will apply to the center of a reservoir, while the push will apply to the bottom of a reservoir.
The shear method has separate cavities split by metallic plates. These vertical plates are heated and create a pressure gradient to force the ink out of the print head.
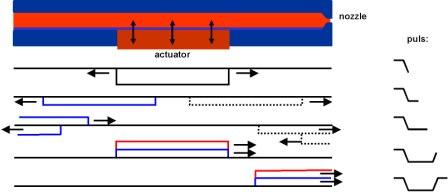
Actuator and relative pulses required for DOD Inkjet printing.
When choosing between the different methods, print head manufacturers have to decide whether or not the ink can withstand different temperatures and pressures, because that is the main difference in applications between these methods.
How Piezo Print Heads Function
A commonality between each of these methods of piezo printing is that the heating of metal plates around the nozzles heats the ink to a point where the ink creates a pressure gradient in the print head. The above examples only differentiate as to where the heat is applied and where the pressure gradient originates. All of the piezo printing technologies creates a pressure gradient so as to expel the ink out of the nozzles at each burst of heat applied.
After the heat is applied in the form of an electric voltage, a drop is fired. A wave of ink equal to the expelled is then reflected back at the reservoir to create a wave of positive pressure, which is then amplified by the second waveform that is created when the next droplet is fired out of the print head.
An actuator for each piezo print head is the electrical element that applies the voltage across the channel.
An electric voltage on a piezo heating element enlarges a channel to generate a large negative pressure in the printing lines and the print head itself. After reflection at the reservoir, this becomes a positive-pressure wave. The positive-pressure wave is amplified by the second slope of the driving waveform to obtain a large positive-pressure peak at the nozzle, which fires a droplet. There are many mathematical equations that can adequately describe this nature, but what can be taken away from this type of printing is the following:
- The charging of a piezo element will enlarge the cross sectional channel, which initiates the negative pressure wave. The negative pressure wave will propagate through the print head and bounce back to the front of the nozzles.
- The reservoir acts as an opene ended channel in order to send a return wave to the front of the nozzles.
- Upon discharge of the piezo printing element amplifies the wave thus increasing the positive pressure.
- The channels are designed to handle a large incoming positive pressure peak at the nozzle.
- The above combine together to release a droplet of ink from the print head.
Inkjet Printing Technologies
After the 1990’s inkjet had worked its way into nearly all households through its printing presence in consumer benchtop printers as a low cost, reliable, fast, and convenient method for printing anything from digital files, photos, or screen shots. It has come a significant distance since its advent in the 1950s, in commercial products such as medical strips and chart recorders. As the industry has seen success the technology spread throughout the 1970s, into the widely recognized printing technique that exists today.
In theory, inkjet printing is simple. A print head ejects micro droplets of ink, carrier, and water onto a substrate (paper, vinyl, PET, etc.). When executing these techniques, companies have spent decades and countless millions practicing their disciplines in this skill. Piezo and thermal print heads are the most common when it comes to jetting UV inkjet or water based latex inkjet ink.
Taking into account the complexity of the practice of inkjet printing, what drives the industry to adopt these techniques is the wide range of applications that are available. Initially, it was seen as a drop on demand product, which can produce any color gamut available without pre-blended colors or a unique colored thermal transfer ribbon. As this technology continues to develop, it is turning into a wider range of applications including educational and industrial where professionals need to accurately deposit precise amounts of materials. Additionally, inkjet printing laid the ground work for the 3d printing technology that is still premature and developing today. The list of industrial uses for inkjet technology appears endless and is only being improved by reduced manufacturing costs, higher quality materials (such as outdoor durable jetted materials, 3d printed materials, and accurate doses), printing on difficult surfaces, reduction of waste, and rapid prototyping.
Application |
Benefits of Inkjet |
Automotive coatings | Replaces spraying or dipping, thereby reducing waste and increasing coating uniformity. |
Plastic part decoration | Non-contact accommodates curved surfaces. Improved print quality over pad or screen printing. Digital eliminates requirement for inventory of screens or pads, resulting in faster prototyping and wider variety of designs. Process color capability reduces the number of ink colors that must be stocked. |
Conductive patterns | Minimizes waste of costly materials; very suitable for short runs. |
Rapid Prototyping | Rapid formation of three-dimensional structures designed by using computer software. |
Variable information | Allows fast changing of the printed information, unlike analogue printing methods which require formation of new hardware (e.g., screens in silk screen printing). |
Ceramics | Minimizes setup time, eliminates requirement for inventory of screens. |
(Magdassi, 2009)
The introduction of inkjet printing in industrial markets has proven to increase manufacturing environments with often more than a modest improvement, or in some cases revolutionize the production and identification of materials and products.